製造・検査工程
当社では、製品の組み立ては設計図面に基づき、各部品を正確かつ丁寧に組み立て、検査を行っています。
不具合を早期発見・修正を行い、システム全体の動作チェック・機能検査・パフォーマンス評価を実施しています。製品が仕様や性能基準を満たしているか確認し、最終的に品質評価を経て出荷を行っています。安心かつ安全にお使いいただけるよう日々製造・検査をしています。
製造工程の各段階で徹底した品質管理を行い、製品の信頼性向上に努めており、各部品の精密な寸法測定や組み付け精度のチェックを行い、不良の発生を未然に防ぎます。また、組み立て後にはテストなどを実施し、長期間の安定稼働を保証できるかを検証しています。
加えて、環境負荷の低減や省エネルギー化にも配慮し、持続可能な生産体制を確立しています。お客様の用途やカスタマイズ要望にもできる限り柔軟に対応し、最適な仕様での納品を実現します。当社は、高い技術力と品質管理体制を活かし、安全で高性能な製品をお届けすることをお約束します。
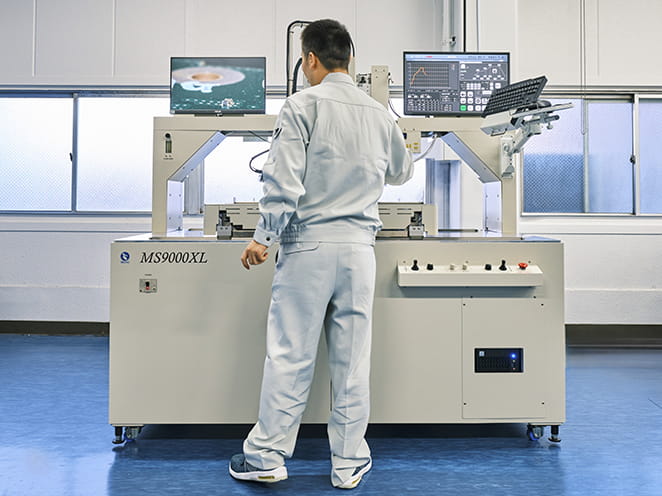
設計
process原材料の受け入れ・品質チェック
設計図面に基づいて製造された部材・部品の受入検査を実施しています。
はじめに、各部材・部品が設計図面と一致しているのかを確認し、寸法や加工精度も確認しています。必要に応じて三次元計測機を使用し、高精度な測定を行った後、規定基準を満たしているかどうかの確認も行います。もし、不具合が発見された場合は、品質管理を徹底するために、迅速な対応を心掛けています。
また、設計開発部門も含めたチームで問題解決に取り組むこともあります。数を確認した後、各材料を製造ラインに供給する準備を整えることを常に意識しています。加えて、部材調達・工場内部での部材加工・内製部品の製作などを実施し、在庫とあわせて調達は計画管理を徹底しています。そのため、製造計画に支障が出ないよう、安定供給を常に維持しています。
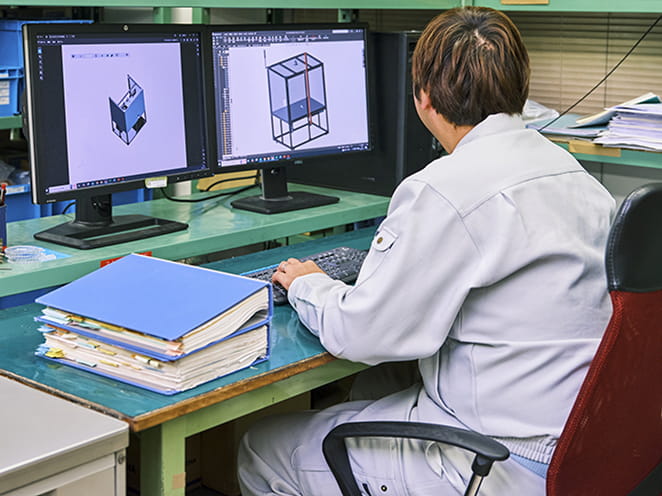
製品組み立て・工程管理
製品組み立ては、各部品が設計図面に基づき、正確に組み立てられるよう慎重に行っています。
部品取り付けや接続作業は、高度な技術と注意が必要なため、組み立て作業中には、各工程ごとに動作・品質チェックを必ず行い、不具合を早期発見・修正できるよう徹底しています。
また、作業スケジュールを厳守し、効率的な生産を維持することを意識しています。各工程管理では、進捗を「見える化」することにより、監視・管理を徹底しています。もし、問題が発生した場合は、製造データの記録と分析を素早く行い、改善点を洗い出し、製造プロセスの最適化に迅速に着手することを常に行っています。
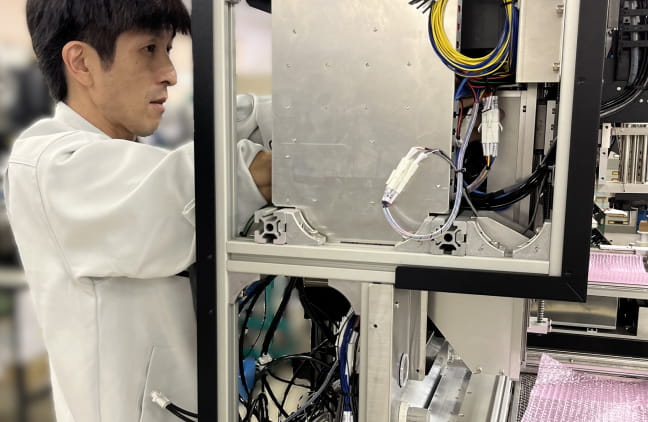
機能検査・パフォーマンス評価
製品組み立てが完了した後、最後に外観検査・システム全体の動作チェックを実施しています。
各機能が正常に動作するのかを確認し、不具合がないことを✓しています。動作チェック完了後に具体的な機能検査に移行し、各機能動作が設計仕様と一致しているかを詳細に検証していきます。
また、パフォーマンス評価では、製品に要求される性能基準を満たしているかをテストしています。負荷試験や耐久試験を行い、製品の信頼性を十分に確認します。そして、最終的に品質評価をクリアした製品のみを出荷するという流れを維持しています。満足していただける製品づくりを万全の態勢で日々行っているため、安心して使用していただきたいと思っています。
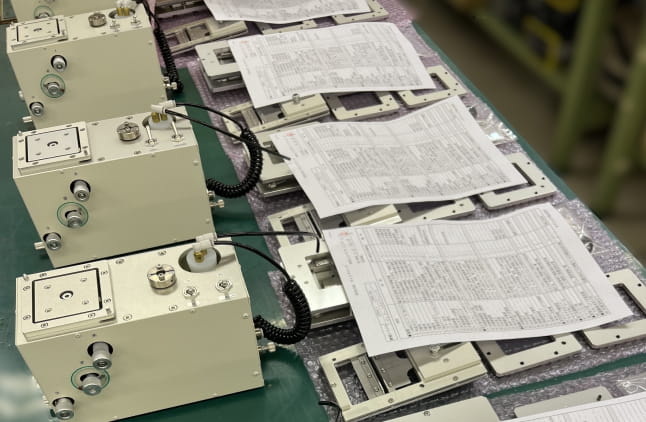
担当者からのご提案
信頼性のある製品提供
当社の製造検査工程は、品質を最優先に考えた厳格なプロセスを実施しています。原材料の受け入れ時に徹底的な検査を行い、製造過程では各工程ごとに品質チェックを行っています。最終的な完成品は、検査チームによる詳細検査を経て、基準に合格したものだけが出荷されます。このように、製造から検査までの全ての工程において、品質管理を徹底することで、お客様に信頼される製品をお届けしています。
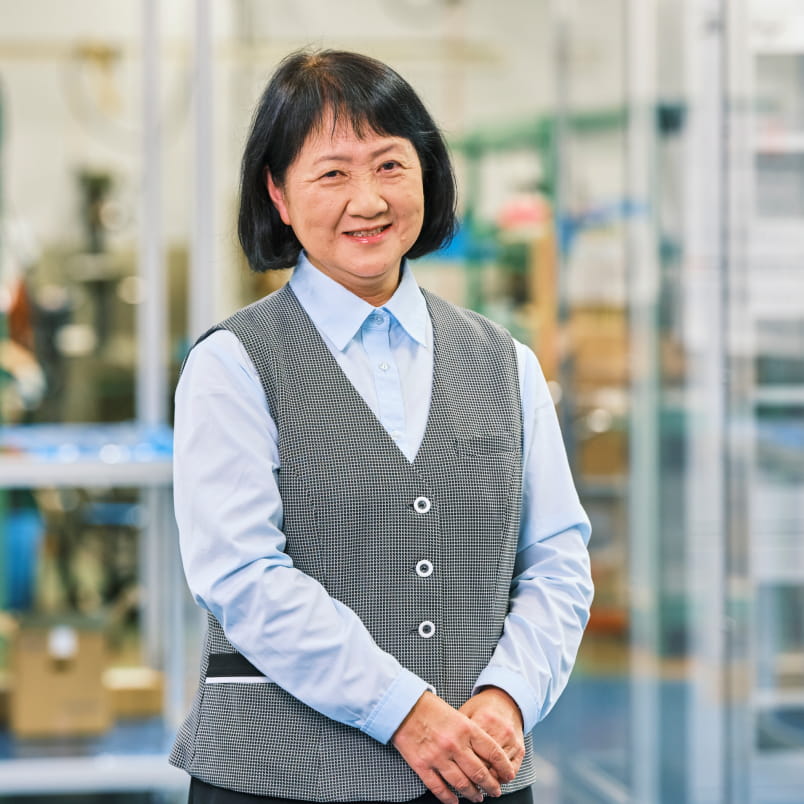