SPI はんだ印刷検査装置
SPI Appearance Inspection Equipment最新のエレクトロニクス製品では、基板上のコンポーネントがますます小型化かつ高密度化しています。このような悩みに対応可能な装置を提案可能で、印刷後の状態を3Dで正確に検査したいという要望に応えた最新の装置を紹介します。
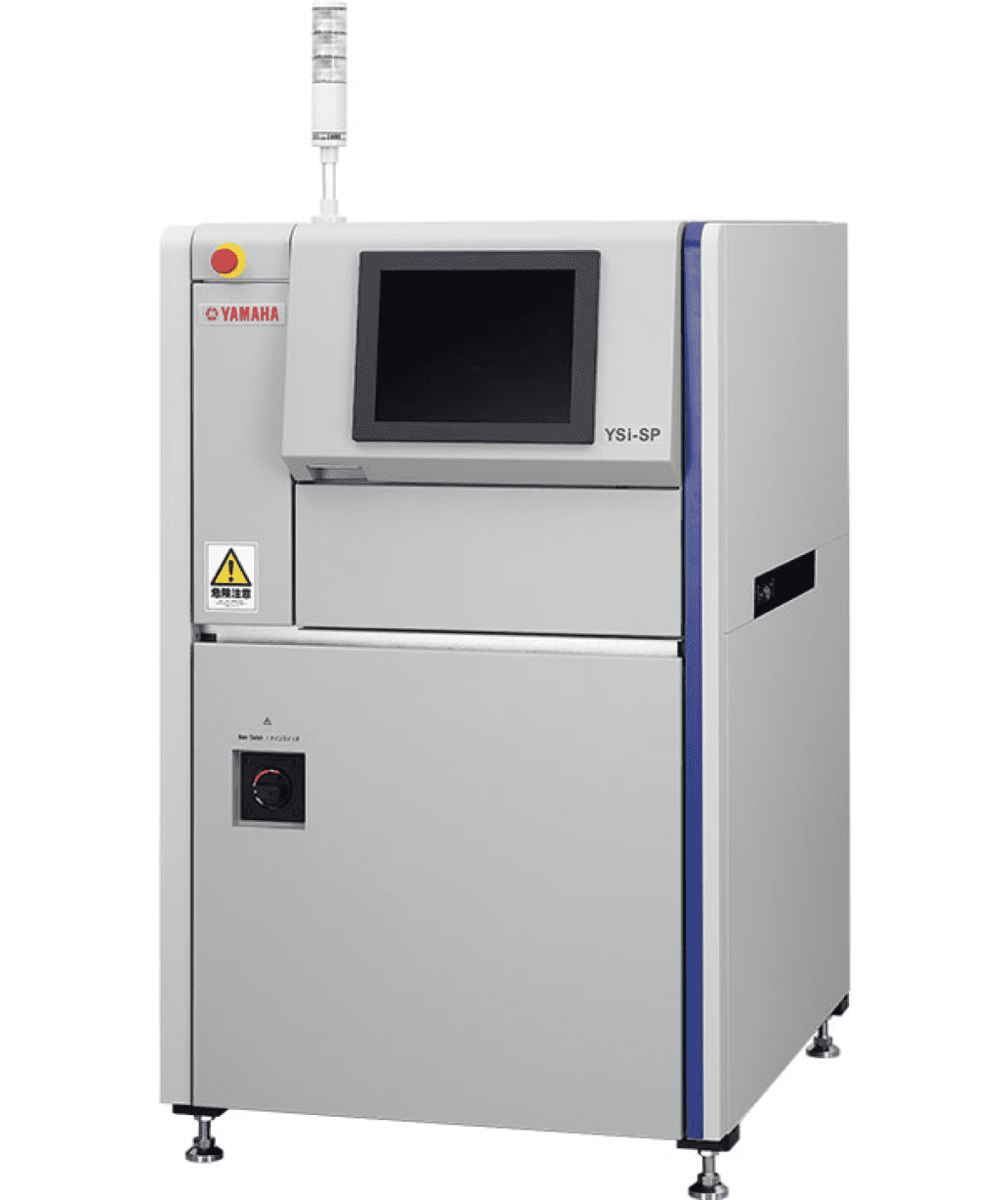
SPI はんだ印刷検査装置とは
about SPI Appearance Inspection EquipmentSPI(Solder Paste Inspection はんだ印刷検査装置)とは、基板上に印刷されたはんだペーストの量・位置・形状を高精度に測定して検査する装置です。
後工程で印刷不良による問題を引き起こすのを未然に防ぎ、生産効率と製品品質の向上に貢献することが役目の設備です。リアルタイムでデータを収集し、印刷プロセスのトレンドや潜在的な問題を分析することも可能です。そのため、装置の設定変更や工程改善を迅速に行うことができるようになり、信頼性の高い基板実装を支える重要なツールと言えます。
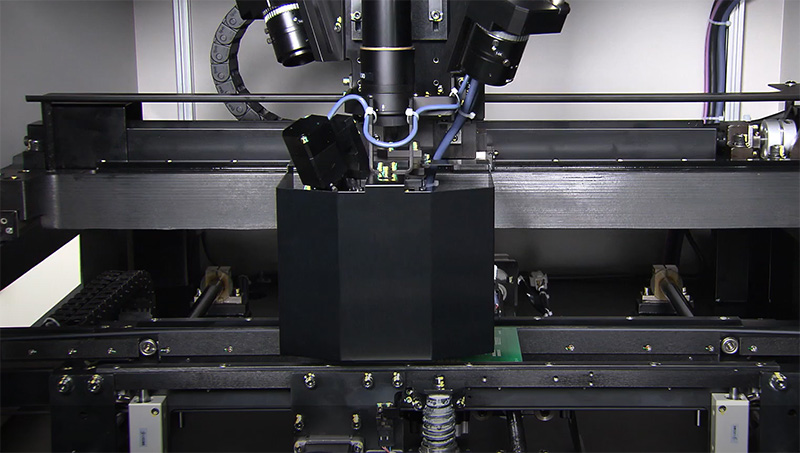
SPI はんだ印刷検査装置の種類
types of SPI Appearance Inspection EquipmentSPIの装置には、大きく分けて2D・3Dの2種類があります。
2DのSPIは、はんだペーストの位置や形状を素早く検査することを得意としています。一方、3DのSPIは、はんだの高さや体積を正確に測定することができ、印刷不良をより詳細に検知することが可能です。高密度化が進む基板実装においては、3DのSPIにおける精度が求められる場面が徐々に増えている現状もあります。
また、オフライン検査タイプ・インライン検査タイプにも区分けすることができます。オフラインタイプは特定の検査対象をじっくり分析したいときに活用され、インラインタイプは生産ラインに組み込んで高速かつリアルタイムで検査を行う量産に活用されています。
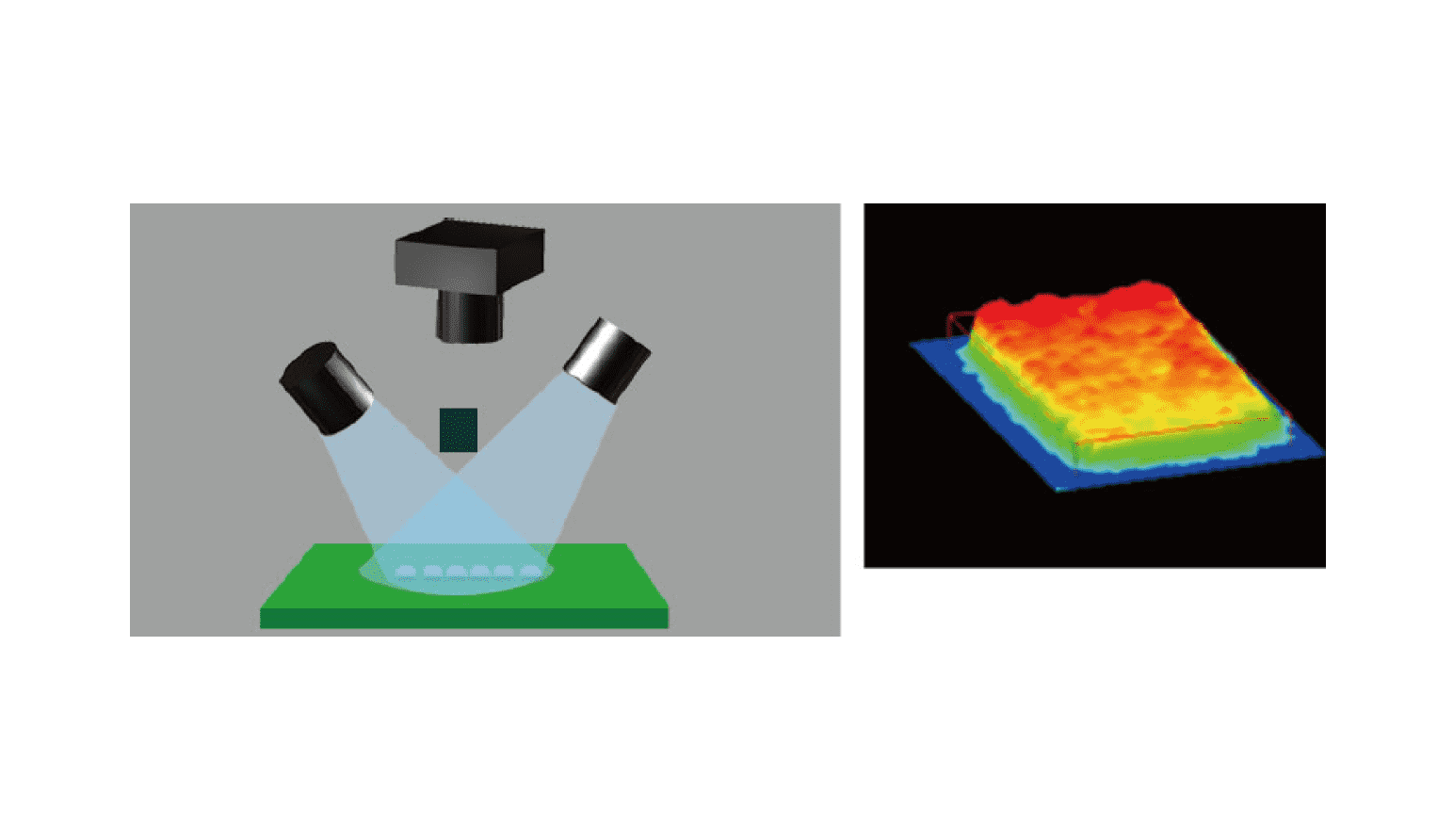
SPI はんだ印刷検査装置のメリット
MERITはじめに、印刷不良を迅速かつ正確に検知できるメリットがあります。はんだペーストの高さや体積、位置のズレなどを数値化して測定することから、肉眼や簡易的な検査では見落とされる不良を早期に発見し、品質を維持することに繋がります。
また、生産ラインのリアルタイムモニタリングを実施できるため、異常の兆候を早期に把握できます。トラブルシューティングを迅速に行うことにより、製造停止や再作業によるコストを抑え、検査データの蓄積と分析を行ってプロセスの継続的な改善も可能です。
これらのメリットは高密度化や微細化が進む基板製造において特に重要であり、品質精度と効率に大きく貢献しています。
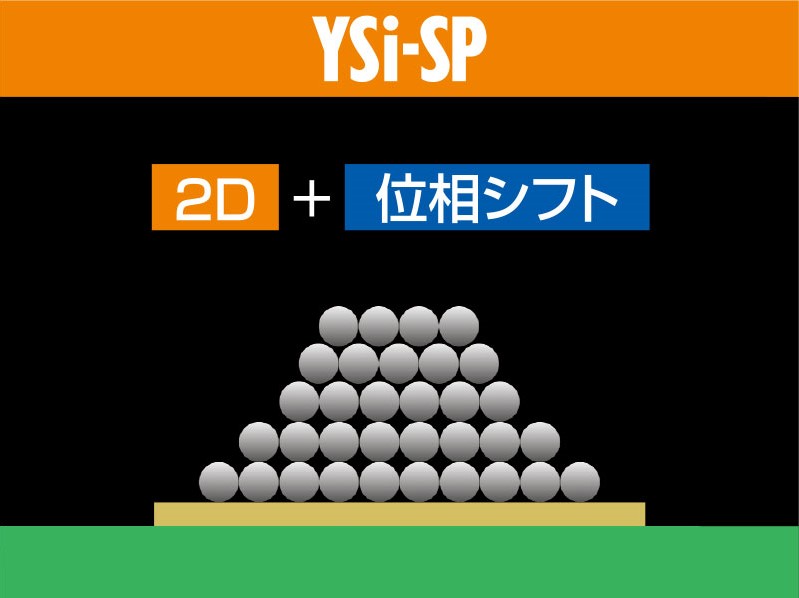
SPI はんだ印刷検査装置に用いられる技術
technology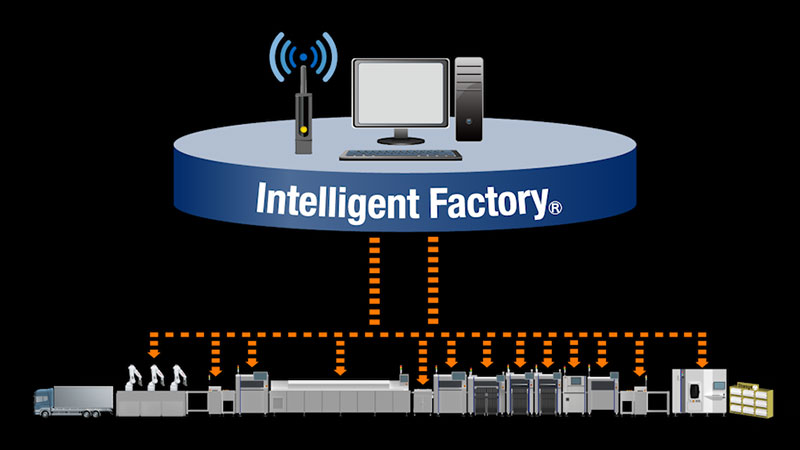
主な技術として、はじめに3D測定技術が挙げられます。
基板上に印刷されたはんだペーストの高さや体積・形状を3次元で解析し、2次元の検査では見逃される可能性が高い不良箇所についても検出することができます。
また、解像度カメラ技術も採用されており、印刷精度や微細な欠陥を正確に可視化することが可能です。そのため、微小な部品や高密度基板でも正確な検査ができます。加えて、リアルタイムデータ処理技術を用いることによって、生産ライン上での迅速な異常検知が実現し、製造ラインの停止を最小限に抑えながら、生産効率を維持することができるようになりました。
SPI はんだ印刷検査装置を上手に使うノウハウ
know-how最も重要なポイントは、検査基準を細かく設定し、製品ごとの要件に応じて適切なしきい値を調整することです。
高密度実装の基板では、微細なはんだ量の検査を必要とする場合があることから、許容範囲を精密に設定することで欠陥検出率を高めることができます。さらに、提供される3D測定データを活用し、印刷条件やステンシルデザインなどの改善を行うことにより、不良低減をより追求することも可能です。
また、自動補正機能を搭載した装置では、何か問題が発生した場合に情報を素早く印刷機へフィードバックし、初期段階での問題を解決を実現し、ライン停止のリスクを抑えることができます。加えて、定期的なメンテナンスやキャリブレーションも実施し、検査精度を維持することも重要です。特にノズルやカメラの状態には注視し、安定したパフォーマンスを確保することでライン全体の効率と品質を最大化することが可能です。
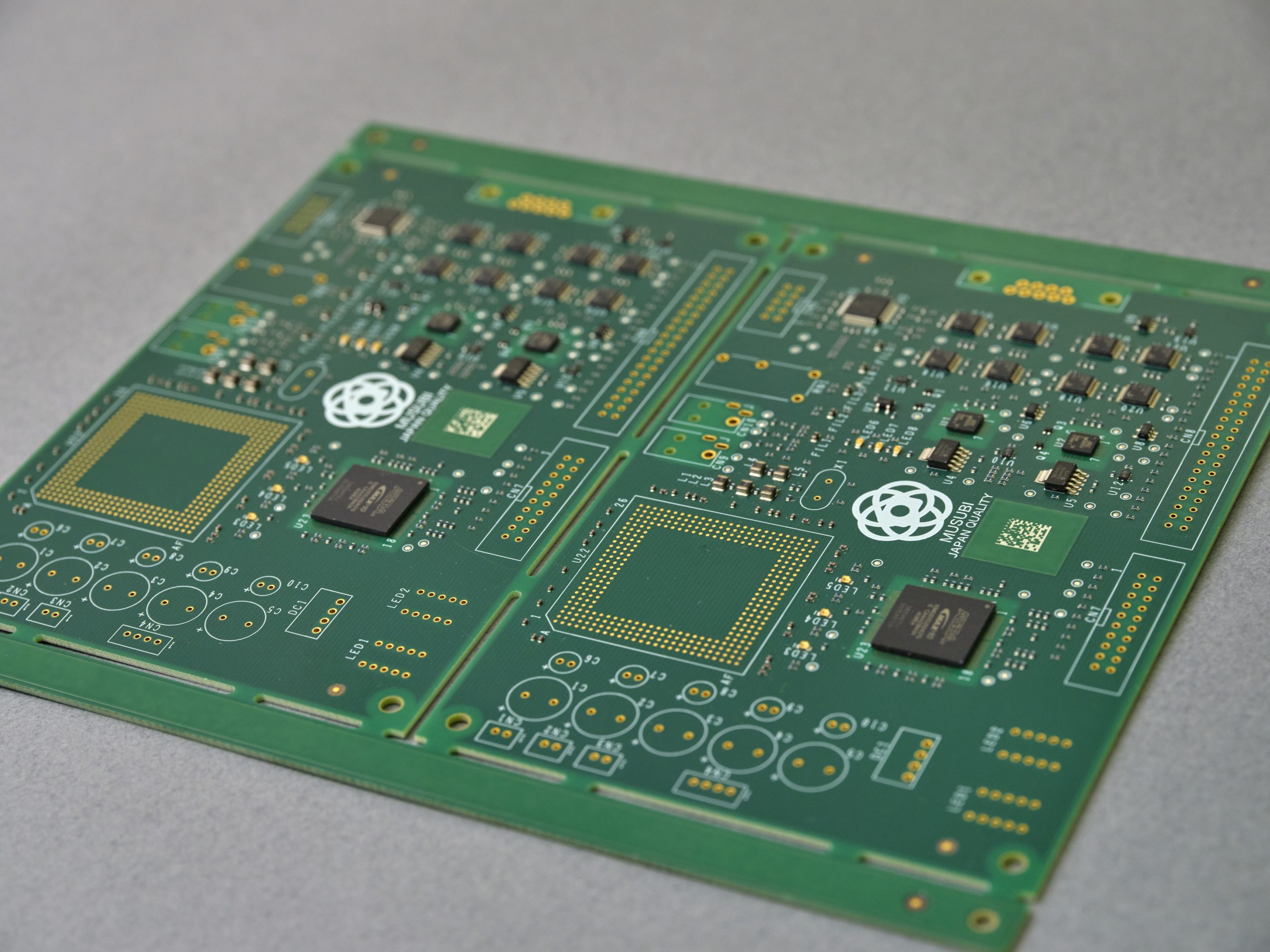
担当者からのご提案
SPI はんだ印刷検査装置導入のご提案
基板の印刷工程後に発生する不良を早期に検出するためには、SPIを活用してはんだ量・配置精度などをリアルタイムでチェックすることが近道です。そのため、印刷の不良やはんだの過剰・不足などを即座に修正し、製品品質の安定を図ることを考えている場合には、導入することは非常に大きなメリットと言えます。
また、基板の特性に合わせて印刷条件を最適化することができ、ラインを停止することなく生産を続けられることも魅力と言えます。
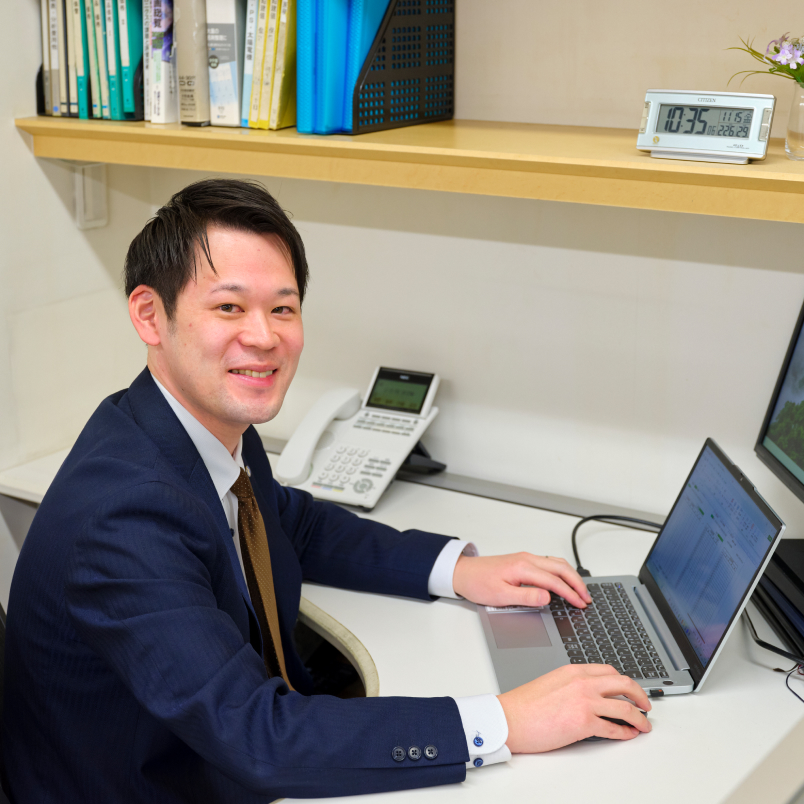